Engineering Services Innovation
Digital Transformation Imperative in Engineering Services
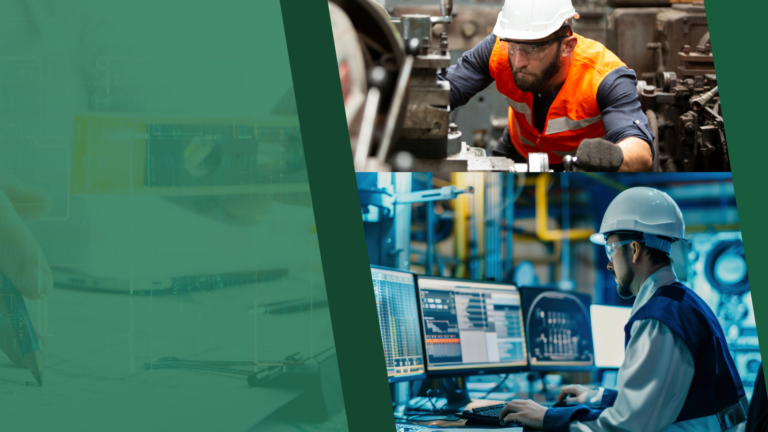
The increasing reliance on digital technologies and processes across engineering services has made digital transformation a critical imperative for staying competitive. This transformation enhances operational efficiency, drives innovation, improves customer experience, and creates new business opportunities.
Defining Digital Transformation
Digital transformation is more than just adopting new technologies. It involves a fundamental shift in how organisations operate, leveraging digital technologies to fundamentally change their business models, culture, and customer interactions.
In engineering services businesses, this means integrating digital technologies and rethinking processes into every aspect of the business, from design and development to manufacturing and maintenance.
Key Benefits of Digital Transformation
The benefits of digital transformation for engineering services services businesses are substantial. By embracing digital technologies, they can:
- Enhance customer experience: Deliver personalised services, improve communication, and increase customer satisfaction.
- Drive innovation: Develop new products and services, explore new markets, and gain a competitive edge.
- Improve operational efficiency: Streamline processes, reduce costs, and increase productivity.
- Increase agility: Adapt quickly to changing market conditions and customer needs.
- Improve decision-making: Leverage data analytics to make informed decisions and optimise operations.
- Enhance sustainability: Reduce environmental impact and promote sustainable practices.
Some Examples of How Digital Transformation Drives Value
Many engineering services businesses have successfully implemented digital transformation initiatives to enhance customer experience. For instance, SKF, a leading bearings and seal manufacturer, uses IoT technology for predictive maintenance. By connecting sensors to machines, SKF can monitor real-time performance and predict potential failures, reducing downtime and optimising maintenance schedules.
Similarly, Bentley Systems has developed digital twin technology to create virtual replicas of physical assets. Digital twins enable real-time monitoring, analysis and simulation, optimising asset performance and improving decision-making.
Enhanced Customer Experience
Digital transformation has revolutionised how engineering services interact with their clients. Leveraging advanced technologies has allowed engineering services businesses to deliver a more personalised, efficient, and transparent customer experience.
The Role of Digital Technologies
Digital technologies play a crucial role in enhancing customer satisfaction. For example, online portals and mobile apps allow clients to track project progress, access project documents, and communicate directly with their engineering teams in real time. This level of transparency fosters trust and builds strong relationships.
Real-time Updates and Predictive Insights
One of the most significant benefits of digital technologies is the ability to provide real-time updates and predictive insights. By leveraging data analytics, engineering services businesses can monitor project performance, identify potential issues, and proactively address them before they escalate. This improves project outcomes and demonstrates a commitment to customer satisfaction.
Not a Choice, But a Necessity
Digital transformation is essential for engineering services businesses looking to deliver exceptional customer experiences. By leveraging digital technologies and adopting a data-driven approach, engineering services businesses can improve transparency, provide real-time updates, and deliver personalised services that exceed customer expectations.
Data-Driven Capabilities
Data has become the lifeblood of modern engineering services businesses. By harnessing the power of data analytics and machine learning, these organisations can gain valuable insights into their operations, optimise processes, and drive innovation.
The Power of Data Analytics and Machine Learning
Data analytics and machine learning enable engineering services businesses to extract meaningful information from vast datasets. By analysing historical data, identifying patterns, and making predictions, these technologies can help organisations:
- Optimise resource allocation: Identify areas where resources are underutilised or overutilised.
- Improve quality control: Detect defects and inconsistencies early in the production process.
- Enhance decision-making: Provide data-driven insights to support strategic planning and problem-solving.
Key Applications of Data-Driven Insights
Data-driven insights can be applied across various areas of engineering, including:
- Predictive maintenance: Use historical data to proactively predict equipment failures and schedule maintenance.
- Optimisation: Identify opportunities to improve efficiency, reduce costs, and enhance performance.
- Product development: Analyse customer data to develop products that meet market needs and preferences.
- Risk management: Assess potential risks and vulnerabilities to mitigate their impact.
Challenges and Opportunities in Data Management and Privacy
While data-driven capabilities offer significant benefits, they also present challenges. Some of the key challenges include:
- Data quality: Ensuring data accuracy, completeness, and consistency.
- Data security: Protecting sensitive data from unauthorised access and breaches.
- Data privacy: Comply with data privacy regulations and protect customer privacy.
Despite these challenges, data management and privacy can be effectively addressed through appropriate strategies and technologies. By investing in data governance, implementing robust security measures, and adopting privacy-enhancing technologies, engineering services businesses can unlock the full potential of data-driven insights while safeguarding sensitive information.
Automation and Efficiency
Automation is a cornerstone of digital transformation in engineering services, offering significant benefits such as increased productivity, reduced costs, and improved efficiency. By automating repetitive tasks, engineering services businesses can free their employees to focus on more strategic and value-added activities.
Identifying Tasks Suitable for Automation
To maximise the benefits of automation, it is essential to identify tasks that are well-suited for automation. These typically include:
- Repetitive and routine tasks: Activities that involve repetitive, manual processes, such as data entry, document generation, and quality control checks.
- Error-prone tasks: Tasks prone to human error include data entry, calculations and analysis.
- Time-consuming tasks: Activities that consume significant time and resources, such as design optimisation or simulation.
Benefits of Automation
Automation offers numerous benefits to engineering services businesses, including:
- Increased productivity: By automating repetitive tasks, engineering services businesses can significantly improve their productivity and output.
- Reduced costs: Automation can reduce operational costs by eliminating manual labour and minimising errors.
- Improved accuracy: Automated systems are less prone to human error, ensuring greater accuracy and reliability in engineering processes.
- Enhanced decision-making: Automation can provide valuable data and insights that can inform better decision-making.
Technologies Used for Automation
A variety of technologies can be used to automate tasks in engineering services, including:
- Robotics: Robots can automate physical tasks, such as assembly, welding, and inspection.
- Machine learning: Machine learning algorithms can be trained to automate tasks involving data learning, such as predictive maintenance or quality control.
- Artificial Intelligence (AI): AI can be used to automate cognitive tasks, such as data analysis, pattern recognition, and decision-making.
- Generative Artificial Intelligence (Gen AI): Gen AI can assist with tasks such as content creation, document summarisation, and document review or comparison.
- Process automation: Software technologies that automate workflows and processes, such as document management and project scheduling.
By strategically implementing automation technologies, engineering services businesses can reap the benefits of increased efficiency, reduced costs, and improved quality while allowing their team members to focus on more value-added strategic activities.
Convergence of IT, OT, ET, and CT
Digital transformation in engineering services requires a holistic approach integrating various technologies to create a unified and efficient system. This convergence involves combining Information Technology (IT), Operational Technology (OT), Engineering Technology (ET), and Consumer Technology (CT).
Understanding the Different Technologies Involved
- IT: Refers to the technology used to process, store, and transmit corporate information such as finance, human resources, and procurement. This includes software, databases, computers, storage, and networks.
- OT: This is used to control and monitor industrial processes, such as manufacturing equipment, sensors, and real-time control systems.
- ET: Encompasses the specialised engineering technologies and software used for design, analysis, and simulation. This includes CAD/CAM software, finite element analysis technologies, and simulation software.
- CT: Consumer-oriented technologies refer to technologies and platforms designed for customer interaction and data management. These include customer relationship management software (CRM), customer data platforms (CDP), data management platforms (DMP), marketing and advertising software, and hardware like smartphones, tablets, and wearable devices. These technologies aim to improve customer experiences and enable remote monitoring and control.
Challenges and Opportunities in Integrating These Technologies
Integrating IT, OT, ET, and CT presents several challenges, including:
- Data silos: Different technologies often operate in silos, making it difficult to share and analyse data.
- Security concerns: Integrating diverse technologies can increase the risk of cyberattacks and data breaches.
- Legacy systems: Many engineering services businesses rely on legacy systems that may need to be compatible with newer technologies.
However, the convergence of these technologies also offers significant opportunities:
- Improved efficiency: By integrating data from different sources, engineering services businesses can optimise processes and reduce costs.
- Enhanced decision-making: Real-time data and analytics can enable better decision-making and problem-solving.
- Innovation: The convergence of technologies can foster innovation and the development of new products and services.
Best Practices for Successful Integration
To successfully integrate IT, OT, ET, and CT, engineering services businesses should follow these best practices:
- Develop a clear strategy: A well-defined strategy outlines the goals and objectives of the integration effort.
- Invest in cybersecurity: Robust security measures are essential to protect sensitive data and prevent cyberattacks.
- Choose compatible technologies: Ensure the chosen technologies are compatible and can be integrated seamlessly.
- Prioritise data management: Develop effective practices to ensure data quality and consistency.
- Foster collaboration: Encourage collaboration among IT, OT, ET, and CT teams to ensure successful integration.
By following these best practices, engineering services businesses can harness the power of technology convergence to drive innovation, improve efficiency, and enhance customer experiences.
Cultural and Organisational Change
Digital transformation is not just about technology; it also requires a fundamental shift in organisational culture. A digital-first mindset is essential for engineering services businesses to thrive in the modern business landscape.
The Importance of a Digital-First Mindset
A digital-first mindset means prioritising technology and data-driven decision-making in all business aspects. It also involves embracing innovation, experimenting with new technologies, and being open to change. Engineering services businesses with a digital-first mindset are better equipped to adapt to the rapidly evolving technological landscape and seize new opportunities.
Strategies for Fostering a Culture of Innovation and Adaptability
To foster a culture of innovation and adaptability, engineering services businesses should:
- Encourage experimentation: Create a safe environment where employees can experiment with new ideas and technologies without fear of failure.
- Promote continuous learning: Invest in employee development and training to ensure they have the skills and knowledge needed to succeed in a digital age.
- Foster collaboration: Encourage collaboration across teams and departments to break down silos and promote knowledge sharing.
- Celebrate success: Recognise and reward employees who contribute to digital transformation initiatives.
Overcoming Resistance to Change and Ensuring Employee Buy-in
Implementing digital transformation can be challenging, and it is essential to address resistance to change. Here are some strategies for overcoming resistance and ensuring employee buy-in:
- Communicate: Effectively communicate the benefits of digital transformation and the reasons for the changes.
- Involve employees: Give employees a voice in the transformation process and involve them in decision-making.
- Alley Fears: Share a sense of safety that digital transformation is not about replacing jobs, but rather an effort to make their jobs easier. Explain how it will help to reduce grunt work and be able to focus on more important things in the business. Don’t forget to explain how a more efficient business can reward employees better.
- Provide support: Offer training and support to help employees adapt to new technologies and processes. Most importantly, give them time and space to learn, away from their day job.
- Celebrate milestones: Recognise and celebrate progress to maintain momentum and morale.
Cultural and organisational change is a crucial component for the success of any digital transformation effort. By fostering a digital-first mindset, promoting innovation and adaptability, and overcoming resistance to change, engineering services businesses can create a culture that supports successful digital transformation and drives long-term growth.
Conclusion
Recap of Key Strategies
Successful digital transformation in engineering services requires a multifaceted approach. Key strategies include:
- Enhanced customer experience: Leveraging digital technologies to improve transparency, communication, and service delivery.
- Data-driven capabilities: Utilising data analytics and machine learning to gain insights, optimise operations, and drive innovation.
- Automation and efficiency: Streamlining workflows and reducing costs through automation.
- Convergence of technologies: Integrating IT, OT, ET, and CT to create a holistic digital ecosystem.
- Cultural and organisational change: Fostering a culture of innovation, adaptability, and collaboration.
Future Trends and Emerging Technologies
The digital transformation landscape is constantly evolving, with new technologies emerging rapidly. Some key trends to watch include:
- Artificial Intelligence (AI): AI is becoming increasingly prevalent in engineering, enabling tasks such as automated design, predictive maintenance, and natural language processing.
- Generative Artificial Intelligence (Gen AI): Gen AI can assist with tasks such as content creation, document summarisation, and document review or comparison.
- Internet of Things (IoT): IoT devices can collect vast amounts of data, providing valuable insights into asset performance and operational efficiency.
- Cloud computing: Cloud-based solutions offer scalability, flexibility, and cost-effectiveness for engineering services businesses.
- Augmented and virtual reality (AR/VR): AR/VR can enhance collaboration, visualisation, and training in engineering projects.
The Importance of Continuous Learning and Adaptation
However, it is important to consider digital transformation not as a one-time event, but rather an ongoing process. Engineering services businesses must continuously learn and adapt to stay ahead of the curve. This includes:
- Upskilling employees: Investing in employee training and development ensures they have the skills to succeed in a digital environment.
- Experimenting with new technologies: Trying out new technologies and approaches to identify opportunities for innovation.
- Monitoring industry trends: Staying informed about the latest developments in digital transformation and their potential impact on the engineering services industry.
By embracing these strategies and staying committed to continuous learning and adaptation, engineering services businesses can position themselves for long-term success in the digital age.